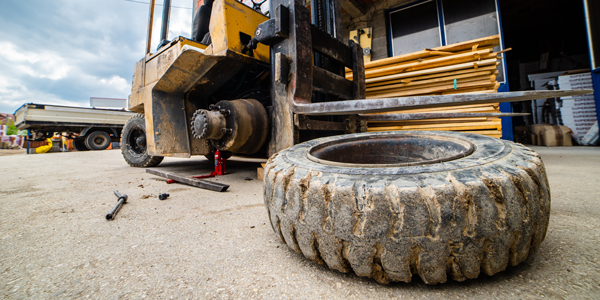
When a tire has been removed from service for an unknown reason, how do you determine the real issue that caused the removal? Most importantly, how do you explain the “why” to the customer? Many times, you are able to inspect the removed tire(s) and make your determination as to why they were removed. But what about the removals for which you are just not sure what happened? How do you handle this situation?
This is a good question and one that I get asked when I am doing a training meeting on tire removals. Many of us who work with off-the-road (OTR) tires have been asked to make decisions and present reasons for removing an OTR tire. But what happens when what you think you see does not match what you have been taught or have seen in the training pictures? This is when the pressure is put on you as the tire expert to properly explain what happened so that the customer understands and accepts your decision.
Over the last few months, I have completed several training programs focused on the root cause of removing OTR tires. This is a great experience for both the people being trained and myself as an instructor. The old saying, “you can’t judge a book by its cover” applies to tires as well. From the outside, you see the result as to why the tire came out of service. But have you really taken the time to determine the real cause so that you can properly explain the reason for failure to your customer? Knowing the real reason for removal will help you either work with the manufacturer if there is an issue with their product or the customer to see what needs to be addressed to ensure the likelihood of repeat failure can be reduced in the future.
History has proven that many tires are removed from service due to cuts and impacts, which eliminates the need to do any further inspection. A cut is easy to detect since you can usually see the external marks on the tire where the object has done damage, which causes the tire to lose air. One must remember that there are times where the damage to the tire does not necessitate the tire to be removed right at that moment. An impact or a rock cut could have damaged the inner construction of the tire. The weakened area will continue to get weaker as the tire remains in service, but it will eventually fail and will need to be removed.
Tires are typically removed after they’ve been “injured,” or have sustained cuts or punctures, when rubber has been pulled away from the wire components. There generally is not any smooth area which represents some type of separation. For a radial tire, the body ply wire still would have rubber on the cable and would show that it was pulled away from the body of the tire. The steel body ply wire or steel belt wire will also be frayed where it broke apart. This generally means there was a rapid air loss incident in or around that area. My findings have been that if the wire ends are smooth and the wire is clean of any rubber, it means there was a separation in that area. The wire flexed more due to the weakened area and eventually broke. This type of injury would resemble a coat hanger being continuously bent back and forth.
Taking the extra steps to explain why you removed a customer’s tire can make the difference in that customer staying loyal to your dealership and the tire manufacturer.
When you have a tire that looks like it was removed due to a separation or a cut, but something just does not look right, what do you do? I imagine most of you would say, “I will call the manufacturer to see what they say and find out if they will warranty the tire.” Hopefully, the manufacturer is proactive, and depending on the size or type of tire, would take time to cut into the tire or allow you to open the area of the injury to see if you can find the real reason for the tire removal.
The reason I am saying this is so that you can learn the real reason for the tire’s removal. Was the tire damaged or did it have a separation? If it did have a separation, was it caused by an external event or a manufacturing issue? Cutting into the tire with a reciprocating Sawzall with a blade used to cut metal will help to determine the cause. Of course, cutting into the sidewall is much easier than the shoulder or tread of the tire, but it can be done by following the groove area of the tire and using a spray bottle of soapy water. Doing this in training classes on a tire removed from service has proven to be extremely educational.
Show and Tell
During one training session, the tire we decided to inspect more closely proved to us that knowing the reason for removal was important. Prior to cutting into the removed tire, we asked, “What happened to the tire?” The answers ranged from low pressure to high heat issues and everything in between. The tire exhibited a blowout in the tread area. The tread belt was sticking out of the tire. Upon closer inspection, the wire ends were frayed and the wire still had rubber on the cable. The belt package and shoulder area had no smooth area representing a separation. The rubber indicated that it was pulled apart, which means a rapid loss of air forced the tire to be pulled apart from its normal state. Also, the liner did not show any signs of being run on low pressure.
We decided to cut into the tire’s shoulder area since it looked like that’s where the incident took place. Knowing where to cut many times is a guess, but once the damaged area is opened you can identify the real issue that took the tire out of service. We were fortunate to have found where an object impacted and damaged the area. Then, by looking closely at the section we cut, we saw where the damage started and spread in the direction the tire was rolling. Eventually, the main area weakened and finally released the air inside the casing.
In this case, the tire was damaged by an external object — not heat, low pressure or a manufacturing issue. Explaining the true reason to your customer as to why the tire was removed takes away any question from your customer’s mind. “Show and tell” is still the best way to properly explain to your customer what it is you are trying to present.
Many times, the customer will listen when you are trying to explain or convince them that the tire was removed due to an operator error. But does the customer “buy in” to your explanation? When you leave, are they still concerned that there could be other issues with the product? This isn’t what you want. If the customer feels there is something you are not telling them, they could start to look for another servicing dealer and tire to support their requirements.
Explaining the true reason to your customer as to why the tire was removed takes away any question from the customer’s mind and ensures that you are looking out for his or her best interests.
We all work hard in gaining the customer’s confidence and trust to work with you and buy the product and services you are selling. Taking the extra steps when a tire comes out of service to explain the reason for removal could make the difference in your dealership keeping that customer — and that customer also staying loyal to the tire manufacturer you represent.
Taking the time to ensure you know what happened to the tire helps show your customer that you are interested in their true costs. They see that you are not just selling them OTR tires and service but are also looking at what needs to be done to address why their tire is out of service. Do you need to do more operator training? Focus on the clean-up of the haul roads, dumps or loading areas? You decide.
Removed tires will tell you a lot, but it is not what you always see on the outside that provides the answer. There are times that you must look closer and dig deeper into the tire to truly understand the reason for removal. Then, you can go to your customer to explain what happened and what needs to be focused on to improve the situation. The time you expend today to take the extra step will provide a higher return tomorrow for you and your customer.
OTR industry veteran Tim Good has spent most of his career in the off-the-road industry, working with Maxam Tire, Goodyear Tire & Rubber Co., among others. His expertise includes major mining, aggregate, construction and port applications.
Check out the rest of the June digital edition of Tire Review here.