When technicians go out on a roadside service call, distracted driving and other on-the-job dangers could play a role in whether they make it to the job site or home safely at the end of the day. To update the industry on best practices to avoid injuries, McCarthy Tire Service and Snider Fleet Solutions welcomed safety representatives from commercial tire dealerships across the country to the third Tire Safety Leadership Summit held in Nashville, Tennessee.
Russ Devens, director of safety and risk management for McCarthy Tire Service, told representatives, “There’s no competition when it comes to safety.” He recognized that while some may be competing, nothing is more important in the industry than the protection of technicians and customers. “[We may sell] Bridgestone, [someone else may sell] Michelin, whatever. Tires are tires, safety is safety.”
Roughly 40 commercial tire industry professionals went to the one-and-a-half-day summit, hosted at Bridgestone Americas’ headquarters, which covered various safety topics relating to the tire industry and fleet tire management. Those included best practices to keep technicians safe during and after service, equipment and technology that promote safety and risk management and how to lead a team to prevent accidents caused by careless service.
Safety During and After Tire Service
Roadside safety and overall technician safety in commercial tire service start with proper training. Kevin Rohlwing, Tire Industry Association’s (TIA) chief technical officer, gave an overview of TIA training and safety practices that should be followed to maintain safety.
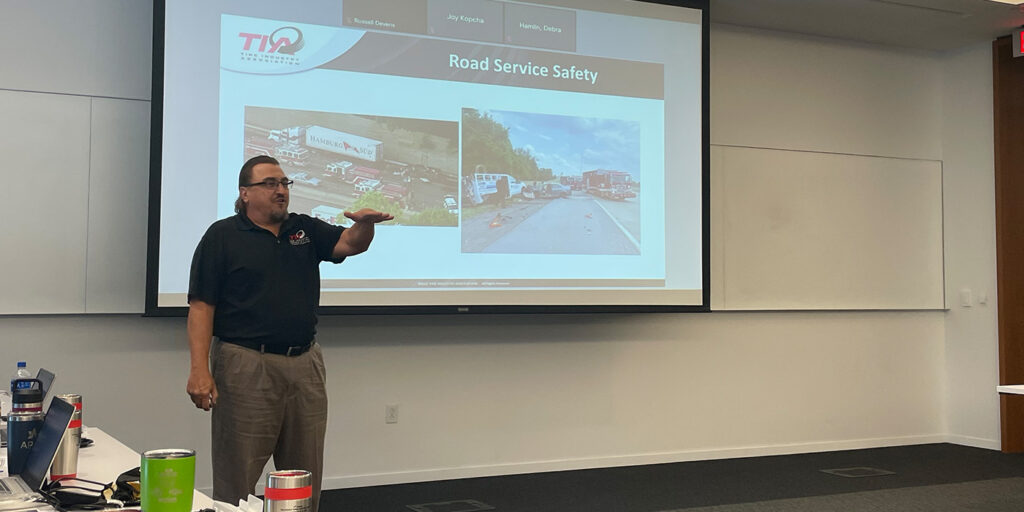
Rohlwing said TIA has updated content for its CTS training videos and described the purpose of the 200- and 300-level courses. He said the 200-level programs now are focused on step-by-step processes for commercial tire and fleet tire service. The 300-level training is focused on the “why” to get technicians to understand the importance of safety processes before, during and after service.
“We changed how we’re doing our training,” said Rohlwing. We can tell [technicians] all day long, ‘You’ve got to do this, you have to do that,’ And some of them aren’t going to agree. But if we can get to them at a higher level of thinking and get them to understand the why behind the safety measures, then they might decide for themselves that this makes sense.”
He described the importance of establishing a baseline standard of care for both tire and wheel inspection and said TIA’s 300-level training courses focus on just that.
Rohlwing also emphasized roadside service safety and informed representatives of TIA guidelines that improve technician and customer safety during tire service, including detailed information on where to park service vehicles and how to make them visible to other drivers.
“You always position the service truck behind the disabled vehicle with the wheels facing straight ahead,” Rohlwing said. “You want to be seen. When the service truck is parked in front of the disabled vehicle, all oncoming traffic sees is a disabled vehicle, not expecting anybody to be working around it. However, if they see a big orange sign or the flashing lights on your service truck, it’s telling them that this is not just a vehicle sitting on side of the road. It is an active work area.”
Tony Nickel, director of captive and special accounts for Federated Mutual Insurance, followed Rohlwing’s presentation with one of his own about automotive claim trends. He discussed the biggest safety issue on the road today – cell phone distraction – and why each dealership’s driving policy should always be on the driver’s mind.

He said in a Harris Poll conducted in 2018, 55% of the 2,000-plus US adults surveyed believed distracted driving was the No. 1 safety threat on the road. “[Close to 90%] admitted to being part of the problem,” Nickel added.
This triggered a discussion on the importance of managing and watching over your roadside assistance fleet drivers with dashcams to make sure they follow company safety standards.
Safety Equipment for Fleet Management and Service
Most dashcams installed in fleets come with software that can report minor driving incidents like hard braking or rolling through a stop and even can detect cell phone usage or if the driver is distracted. Nickel explained how equipping roadside service fleets with a dashcam can create coaching opportunities that come while looking at and reviewing potential incidents with your drivers. He said it’s also a great way to incentivize good drivers and “coaches” who manage the fleet and its overall safety.
“The policies have to be clear,” said Nickel. “What are you doing with your policies? How often are you communicating with your drivers and your entire employee group about them? What are your expectations for various scenarios?”
He said that if dealerships are not regularly communicating their driving policy, he highly recommends it be discussed at least once a year.
Sean McIlhenny, vice president and senior risk manager for Conner Strong & Buckelew Insurance, said dashcams add another layer of protection for drivers. He said similar to wearing safety gloves or the proper footwear, companies should put layers of protection – like a dashcam – in place to increase safety as much as possible. He said that explaining the importance of this technology to employees can help them understand its safety benefits.

He gave four management and leadership steps to communicate to employees regarding all safety procedures:
- Regularly communicate the commitment to a safety and health program.
- Define program goals.
- Allocate the resources.
- Expect performance with accountability.
To round out the sessions on safety equipment, Don Tinker, North America business development manager for AME International, delved into AME’s jacking and cribbing technology and process.
Jacking and cribbing can be a tough process for technicians in the field, since trying to find the best way to lift a vehicle under various conditions can even be dangerous without the right equipment. In the past, oak blocks have been used for such purposes, but Tinker said cribbing has come a long way.

He described AME’s cribbing technology that locks together to prevent slipping. He said this is beneficial for fleet services that need to change a customer’s OTR, Ag or construction tire safely without having to worry about weight imbalance. Each block is individually weight-rated and mechanically locks to the load with an AME jack plate.
“When you’re training on cribbing, it is absolutely imperative that they have, at minimum, a top plate that covers the entire stack,” he said. “This way when they place that top plate on top, it displaces everything across the entire stack.”
Utilize Leadership to Promote Safety
Jim Lanham, safety manager for McCarthy Tire, said communicating with your technicians about safety measures is important because it can not only save their lives but countless others on the road.
Company leadership should incorporate detailed training processes for important roadside procedures like removing and replacing wheels or tires, Lanham said. Through his own research, he found that almost half of accidents following service were due to policy violations, something that could have been avoided with better leadership.
“If our guys don’t put [a tire] on right, or violate another policy, it’s potentially your family – the person you care the most about – that the wheel-off killed,” said Lanham.

Lanham said nothing is more important than technicians and customers coming home safely after service. Following his presentation, the group discussed the importance of taking a leadership role and having managers communicate processes to technicians to keep them accountable. Most agreed that it isn’t enough to have a policy or procedure, but it needs to be managed on-site, face-to-face. They advised that mechanisms be in place that holds employees accountable when policy violations occur to ensure a dealership’s safety procedures are followed.