How do you handle a brake pulsation complaint or comeback? Blame the pads? The driver? Defective rotor? As they say, when you point your finger at any of these items, there are three fingers pointing back at you.
Myth 1: Machining rotors is unprofitable.
Labor in your dealership does not take up inventory and does not have to be delivered by a parts store. You just have to make it a line item on the repair order instead of giving it away with every brake job.
You may think that installing new rotors eliminates the possibility of a comeback. However, this myth creates more comebacks than it solves. These comebacks often start with blaming the new pads and ends with the customer having to return a second or third time until someone pulls out a dial indicator and micrometer.
Installing new rotors is not a way to avoid having to use a micrometer or dial indicator. For every brake job, you should always measure for runout (rotor and flange) and the dimensions of the rotor before brake service is performed.
After a rotor is resurfaced or a new rotor is installed, the new or refinished rotor should be measured for runout when it is installed on the vehicle as a quality control method. A new rotor could show excessive runout when it is installed due to a stacking of
tolerances.
Myth 2: New rotors prevent comebacks and are cheaper and more profitable than using an on-the-car lathe.
In some cases with excessive runout, a new rotor should be machined to match the vehicle. It has often been said that you should never machine new rotors. But, what if the runout exceeds the manufacturer’s specifications when the new rotor is installed on the vehicle? This is when it is permissible to machine a new rotor with an on-the-car brake lathe. This helps to match the rotors to the hub flange.
Using an on-the-car lathe can help to reduce run-out on new rotors. The main advantage of these lathes is that they are able to cut a rotor in its operating plane. This means that the rotor is machined to match the hub.
Myth 3: Rotors do not need to be measured.
Even if you use new rotors, your chance of a pulsation comeback could be greater than if you left the old rotors on the vehicle. Runout in the hub and new rotor can stack up to cause disc thickness variation (DTV) in a few thousand miles. DTV is the main cause of pulsation.
Runout greater than .005-inch (±.001-inch depending on the rotor or flange diameter) is a sign that the flange, rotor and/or bearing should be replaced. The needle of the dial indicator should be perpendicular to the rotor. Measurements should be taken a quarter inch from the edge.
Flange runout can be corrected with tapered shims that are available to correct a runout of 0.003-inch (0.075 mm) to 0.009-inch (0.230-mm). A runout of more than 0.005-inch (0.125-mm) at the bearing flange cannot be corrected by the use of a shim. The combination of rotor and bearing flange could prevent the rotor from being turned. Checking bearing flange runout should be performed after friction surface runout. Changing the rotor position 180 degrees on the bearing can check flange runout. If the high spot changes 180 degrees, the rotor could be OK or ready to turn after the bearing is shimmed.
Myth 4: Two passes make for a better finish.
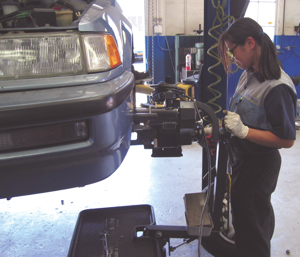
Cutting a rotor in one pass is essential for productivity. For non-composite rotors, it is possible to take as much as 0.020-inch per side while still having an acceptable finish. However, with a composite rotor or one with hard spots, the depth should be reduced, likely below 0.010-inch per side, for a quality finish. In order to remove this much material, it is essential to have sharp bits.
Cutting too fast will reduce the cut quality and possibly create chatter. A larger diameter rotor will need to turn slower than a small diameter one. Single-speed lathes are set at the slower speed of the largest application they are designed to cut. This is usually around 0.002-inch per revolution.
Poor rotor finish can lead to noise. When machining a rotor, you have two primary goals: Provide a smooth surface finish for the pads and provide a true surface finish.
Never use the ballpoint pen measurement method when machining rotors. The only real way to measure is with a profilometer that measures the roughness average. It is very expensive and very fragile.
The best way to make sure a lathe is cutting rotors properly is to make sure your cutting bits are fresh, adapters are true and the cross feed is set as required.